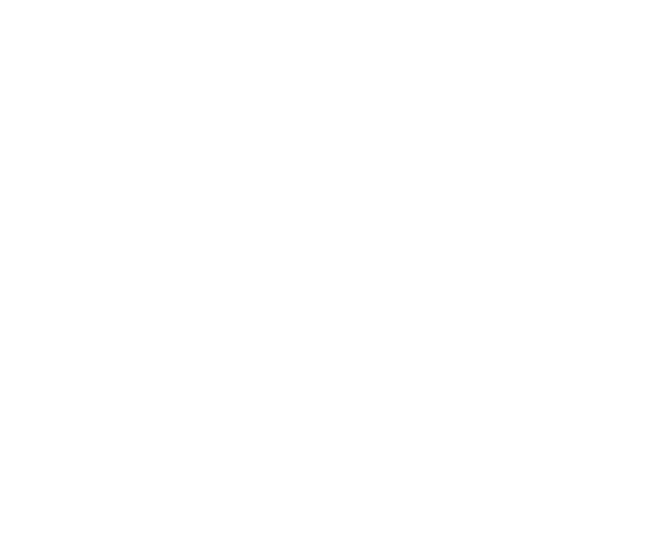
Hank intervient en tant qu’assistant à maîtrise d’ouvrage auprès de clients publics et privés.
Notre mission ? Faire émerger ou reconfigurer des projets urbains et immobiliers dans la perspective d’une architecture augmentée telle que portée par l’agence
Patriarche. Office of Architecture.
Un projet ? Une question ? Écrivez-nous par email à l’adresse info@thinkhank.fr ou via le formulaire de contact.
Un projet ? Une question ? Écrivez-nous par email à l’adresse info@thinkhank.fr ou via le formulaire de contact.